Mastering Bronze Casting for Modern Sculpture Art
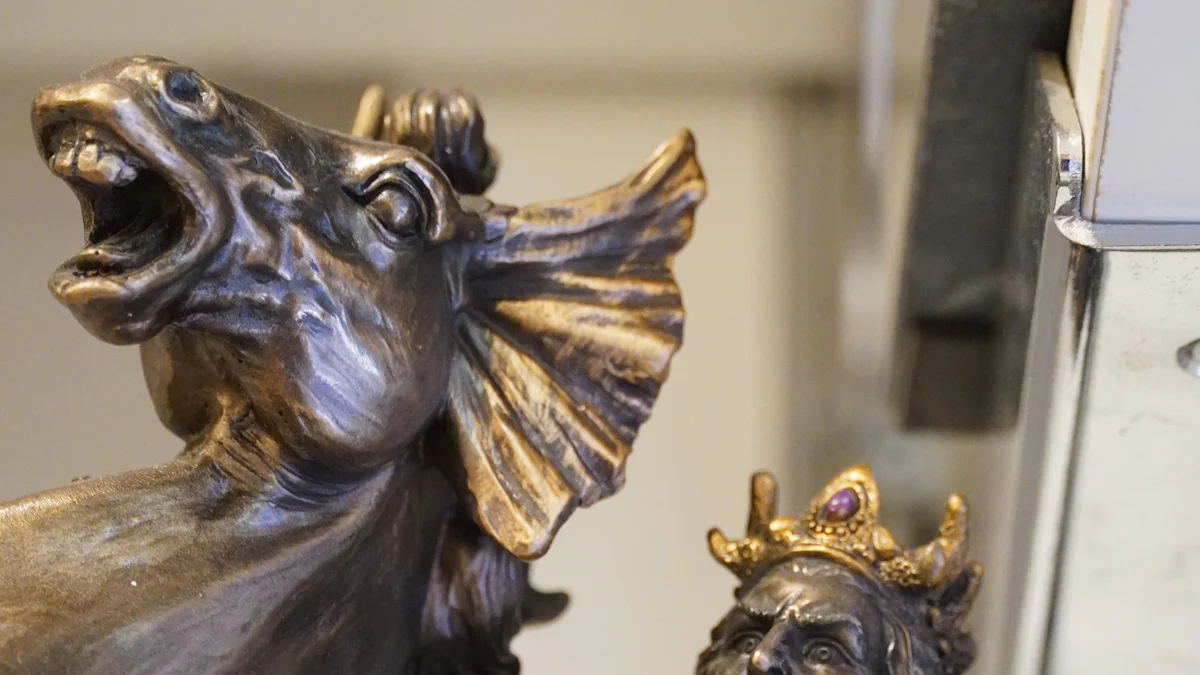
Bronze casting has captivated artists for centuries due to its unique blend of durability and elegance. This ancient craft, which involves pouring molten bronze into molds, allows sculptors to achieve intricate details and lifelike forms. The alloy’s strength and malleability make it ideal for creating everything from monumental statues to delicate figurines. Modern artists continue to push the boundaries of this technique, blending traditional methods like bronze investment casting with contemporary innovations. Bronze castings not only preserve artistic visions but also stand as enduring testaments to human creativity and craftsmanship. In an investment casting plant, artisans meticulously execute these processes, ensuring that each piece reflects the highest standards of quality and artistry.
Key Takeaways
- Bronze casting is a time-honored technique that allows artists to create intricate and durable sculptures, blending traditional methods with modern innovations.
- The lost wax casting method is essential for achieving high precision and detail in bronze sculptures, making it a favorite among artists.
- Beginners should start with simple projects and gradually build their skills, focusing on mastering mold-making and safety protocols.
- Investing in quality tools and materials, such as modeling wax, mold-making supplies, and protective gear, is crucial for successful bronze casting.
- Embrace technology by utilizing 3D modeling and printing to streamline the casting process and enhance creative possibilities.
- Public art installations benefit from bronze’s durability and aesthetic appeal, making it a popular choice for large-scale sculptures in community spaces.
- Continuous learning through workshops, online resources, and mentorship can significantly enhance your bronze casting skills and artistic expression.
What is Bronze Casting?
Bronze casting is a time-honored process that transforms molten bronze into intricate sculptures and objects. This method has been a cornerstone of artistic expression for centuries, enabling creators to craft works that endure both physically and culturally. By understanding its basics and historical significance, one can appreciate the profound impact this technique has had on the art world.
The Basics of Bronze Casting
Bronze casting begins with the creation of a model, often sculpted from clay, wax, or plaster. This model serves as the foundation for the mold, which captures every detail of the artist’s vision. Once the mold is prepared, artisans pour molten bronze into it, filling the hollow spaces. After cooling, the mold is removed, revealing the raw bronze sculpture. Skilled craftsmen then refine the piece through techniques like polishing, patination, and detailing.
The process demands precision and expertise. Each step, from mold preparation to finishing, requires careful attention to detail. The “lost wax” method, one of the most popular techniques, allows for intricate designs and lifelike forms. This method involves coating a wax model in a ceramic shell, melting the wax away, and replacing it with molten bronze. The result is a faithful reproduction of the original model, cast in durable bronze.
Historical Significance of Bronze Casting in Art
Bronze casting has played a pivotal role in art history, shaping some of the most iconic sculptures ever created. In Classical Antiquity, civilizations like the Greeks and Romans used bronze to craft monumental statues, many of which symbolized gods, heroes, and cultural ideals. These works showcased the material’s strength and versatility, cementing its place in artistic traditions.
During the Renaissance, bronze casting experienced a revival. Artists like Michelangelo and Benvenuto Cellini embraced the lost wax method to create masterpieces such as David and Perseus. These sculptures demonstrated the potential of bronze to capture dynamic poses and intricate details, inspiring generations of artists. The Renaissance also marked the spread of bronze casting techniques across Western Europe, leading to a surge in its popularity.
In modern times, bronze casting continues to evolve. Contemporary artists experiment with new forms and technologies while honoring traditional methods. This blend of innovation and heritage ensures that bronze casting remains a vital medium for artistic expression.
The Artistic Process of Bronze Casting
Step-by-Step Guide to Lost Wax Casting
The lost wax casting method, also known as investment casting, is one of the most intricate and widely used techniques in bronze casting. This process begins with the creation of a detailed model, typically sculpted from wax. Artists use wax because it is malleable and capable of capturing fine details. Once the model is complete, they coat it with a ceramic shell, layer by layer, to form a mold. Each layer must dry thoroughly before the next is applied, ensuring the mold’s strength.
After the ceramic mold hardens, artisans heat it to melt and remove the wax, leaving a hollow cavity. This step gives the technique its name—lost wax casting. Molten bronze, heated to approximately 2,000°F, is then poured into the cavity. Once the bronze cools and solidifies, the ceramic shell is carefully broken away, revealing the raw sculpture. Artists then refine the piece through processes like grinding, polishing, and patination to achieve the desired finish.
This method allows for exceptional precision and detail, making it a favorite among sculptors. Its versatility has enabled artists to create everything from small figurines to monumental statues. The lost wax casting process, though labor-intensive, remains a cornerstone of bronze casting due to its ability to faithfully reproduce an artist’s vision.
Alternative Methods: Sand Casting and Direct Casting
While lost wax casting is renowned for its precision, other methods like sand casting and direct casting offer unique advantages. Sand casting involves creating a mold from compacted sand. Artists press a model into the sand to form an impression, which serves as the mold. Molten bronze is then poured into the cavity. This method is faster and more cost-effective than lost wax casting, though it may not capture intricate details as effectively.
Direct casting, on the other hand, skips the mold-making process entirely. Artists carve directly into materials like wax or clay, which are then replaced with molten bronze. This technique is ideal for creating organic, freeform shapes. It allows for spontaneity and experimentation, making it popular among contemporary sculptors.
Both sand casting and direct casting demonstrate the adaptability of bronze casting. These methods provide artists with diverse tools to bring their creative visions to life, whether they prioritize speed, cost, or artistic freedom.
Finishing Techniques in Bronze Casting
The finishing stage transforms a raw bronze sculpture into a polished masterpiece. After removing the mold, artists inspect the piece for imperfections. They use tools like grinders and files to smooth rough edges and refine details. This step ensures the sculpture aligns with the artist’s original design.
Patination is another critical finishing technique. By applying chemical solutions to the bronze surface, artists can achieve a range of colors and textures. For example, ferric nitrate produces warm brown tones, while cupric nitrate creates vibrant greens. Patinas not only enhance the sculpture’s aesthetic appeal but also protect the bronze from corrosion.
Polishing is the final step. Artists use abrasives to achieve a smooth, reflective surface or a matte finish, depending on the desired effect. This stage highlights the bronze’s natural beauty and adds depth to the sculpture.
Finishing techniques play a vital role in bronze casting. They allow artists to personalize their work and ensure each piece is both visually stunning and durable.
Modern Applications of Bronze Casting in Sculpture
Contemporary Artists and Innovations in Bronze Casting
Contemporary sculptors continue to redefine bronze casting by merging traditional craftsmanship with modern artistic visions. Artists like Anish Kapoor and Antony Gormley have embraced this medium to create works that challenge conventional forms and explore abstract concepts. Kapoor’s polished bronze sculptures, for instance, manipulate light and reflection, transforming static objects into dynamic visual experiences. Gormley, on the other hand, uses bronze to explore the human form, often casting life-sized figures that interact with their surroundings.
Collaboration between sculptors and foundries plays a crucial role in these innovations. As Frederic Remington, a renowned sculptor, once noted, “Some of the most remarkable American bronzes are the tangible products of symbiotic collaborations between a sculptor and a foundry.” Foundries provide technical expertise, enabling artists to push the boundaries of what is possible with bronze. This partnership ensures that even the most ambitious designs can be realized with precision and durability.
Innovative approaches, such as combining bronze with other materials like glass or wood, have also gained popularity. These mixed-media creations highlight the adaptability of bronze casting and its ability to complement diverse artistic elements. By experimenting with form, texture, and material, contemporary artists continue to expand the possibilities of this ancient craft.
Technology and Bronze Casting: 3D Printing and Digital Tools
The integration of technology has revolutionized bronze casting, making it more accessible and versatile. Digital tools, such as 3D modeling software, allow artists to design intricate sculptures with unparalleled accuracy. These digital models can be used to create prototypes or molds, streamlining the casting process and reducing the margin for error.
3D printing has emerged as a game-changer in the field. Artists can now print wax or resin models directly from their digital designs, bypassing the need for manual sculpting. This method not only saves time but also enables the creation of complex geometries that would be difficult to achieve by hand. For example, intricate lattice structures or interlocking forms can be printed and then cast in bronze using the lost wax method.
Foundries have also adopted advanced technologies to enhance their processes. Computer-aided design (CAD) and computer-aided manufacturing (CAM) systems ensure precision at every stage, from mold-making to finishing. These tools allow artisans to replicate even the most intricate details, ensuring that the final bronze piece faithfully reflects the artist’s vision.
By embracing technology, bronze casting has entered a new era of innovation. Digital tools and 3D printing have not replaced traditional methods but have instead complemented them, offering artists new ways to bring their ideas to life.
Bronze Casting in Public Art and Installations
Bronze casting has become a cornerstone of public art, offering durability and aesthetic appeal for large-scale installations. Cities around the world feature bronze sculptures in parks, plazas, and cultural landmarks, where they serve as focal points for community engagement. These works often celebrate historical figures, commemorate events, or reflect local culture.
One notable example is the Charging Bull sculpture in New York City’s Financial District. Cast in bronze, this iconic piece symbolizes strength and resilience, drawing millions of visitors each year. Similarly, Louise Bourgeois’ Maman, a massive bronze spider, captivates audiences with its imposing presence and intricate details, showcasing the material’s versatility.
Public art projects often require collaboration between artists, architects, and urban planners. Bronze’s durability makes it an ideal choice for outdoor installations, as it can withstand weathering and environmental factors. Additionally, the patination process allows artists to customize the sculpture’s appearance, ensuring it harmonizes with its surroundings.
Bronze casting continues to play a vital role in shaping public spaces. These installations not only enhance the visual landscape but also foster a sense of identity and connection within communities.
How to Get Started with Bronze Casting
Embarking on the journey of bronze casting can be both exciting and rewarding. This ancient craft, which has been practiced for over 5,000 years, offers endless opportunities for creativity and self-expression. Beginners can start small, gradually building their skills and confidence. Understanding the essential tools, learning resources, and practical tips will help aspiring artists take their first steps into this fascinating art form.
Tools and Materials for Beginners
To begin bronze casting, artists need a basic set of tools and materials. These items ensure safety, precision, and efficiency during the process. Here is a list of essentials:
- Wax or Clay for Modeling: These materials allow artists to create the initial model, which serves as the foundation for the mold.
- Mold-Making Supplies: Silicone rubber or ceramic shell materials are commonly used to create molds that capture intricate details.
- Crucible and Furnace: A crucible holds the bronze while it melts, and a furnace provides the high temperatures needed to liquefy the metal.
- Protective Gear: Safety equipment, such as heat-resistant gloves, goggles, and aprons, protects against burns and other hazards.
- Bronze Alloy: Beginners should choose a standard bronze alloy, which is durable and easy to work with.
- Finishing Tools: Files, grinders, and polishing pads help refine the sculpture after casting.
These tools form the foundation of any bronze casting setup. Beginners should invest in high-quality equipment to ensure consistent results and a safe working environment.
Learning Resources for Bronze Casting
Learning bronze casting requires a combination of theoretical knowledge and hands-on practice. Fortunately, numerous resources are available to guide beginners:
- Workshops and Classes: Many art schools and community centers offer bronze casting courses. These programs provide access to professional equipment and expert instruction.
- Books and Guides: Comprehensive guides, such as Bronze Casting for Beginners, cover the fundamentals of the craft, including techniques like lost wax and sand casting.
- Online Tutorials: Platforms like YouTube and Skillshare feature step-by-step tutorials from experienced artists. These videos demonstrate techniques in an accessible format.
- Foundry Visits: Visiting a local foundry allows beginners to observe the process firsthand. Many foundries also offer mentorship or apprenticeship opportunities.
- Art Communities: Joining forums or social media groups dedicated to bronze casting connects beginners with experienced artists who can offer advice and feedback.
By exploring these resources, beginners can gain a deeper understanding of bronze casting and develop their skills at their own pace.
Beginner Tips for Successful Bronze Casting
Starting with bronze casting can feel overwhelming, but following these tips will help beginners achieve success:
- Start Small: Focus on creating simple designs before attempting complex sculptures. Small projects build confidence and allow for experimentation.
- Plan Carefully: Sketch the design and plan each step of the process. Proper planning reduces errors and ensures a smoother workflow.
- Practice Mold-Making: Perfecting mold-making techniques is crucial for capturing fine details. Beginners should practice with inexpensive materials before using bronze.
- Work Safely: Always wear protective gear and follow safety protocols. Melting bronze involves extreme heat, so caution is essential.
- Seek Feedback: Share work with mentors or peers to receive constructive criticism. Feedback helps identify areas for improvement and inspires growth.
- Be Patient: Bronze casting is a time-intensive process. Rushing can lead to mistakes, so beginners should approach each step with care and attention.
By adhering to these tips, aspiring artists can navigate the challenges of bronze casting and create pieces that reflect their artistic vision.
Bronze casting remains a cornerstone of modern sculpture, celebrated for its ability to capture intricate details and withstand the test of time. Its versatility and durability empower artists to create works that blend tradition with innovation, ensuring its relevance in contemporary art. Aspiring sculptors can explore this craft through small projects or formal training, discovering its potential to bring their creative visions to life. By embracing both the historical significance and modern advancements of bronze casting, artists can contribute to a legacy that continues to inspire and evolve.
FAQ
What is bronze casting, and why is it significant in sculpture?
Bronze casting is a process where molten bronze is poured into a mold to create sculptures or objects. This technique has been a cornerstone of artistic expression for centuries due to its ability to capture intricate details and its durability. Artists value bronze for its strength, versatility, and aesthetic appeal, making it a preferred medium for both historical and contemporary works.
How does the lost wax casting method work?
The lost wax casting method involves creating a detailed wax model, coating it with a ceramic shell, and then melting the wax away to leave a hollow mold. Molten bronze is poured into this mold, and once it cools, the ceramic shell is removed to reveal the sculpture. This method allows for exceptional precision and is widely used by artists to achieve lifelike details.
What tools and materials are essential for beginners in bronze casting?
Beginners need several key tools and materials to start bronze casting:
- Modeling materials like wax or clay for creating the initial design.
- Mold-making supplies, such as silicone rubber or ceramic shell materials.
- A crucible and furnace for melting bronze.
- Protective gear, including heat-resistant gloves, goggles, and aprons.
- Bronze alloy for casting.
- Finishing tools, such as grinders and polishing pads, for refining the sculpture.
Investing in high-quality equipment ensures safety and consistent results.
Can beginners learn bronze casting without prior experience?
Yes, beginners can learn bronze casting through various resources. Workshops, online tutorials, and books provide step-by-step guidance. Visiting foundries or joining art communities also offers valuable insights. Starting with small projects helps build confidence and allows beginners to gradually develop their skills.
What are the safety precautions for bronze casting?
Safety is crucial in bronze casting due to the high temperatures involved. Beginners should always wear protective gear, including gloves, goggles, and aprons. Working in a well-ventilated area minimizes exposure to fumes. Following proper handling procedures for molten bronze and equipment ensures a safe casting environment.
How long does the bronze casting process take?
The duration of the bronze casting process depends on the complexity of the sculpture and the chosen method. Lost wax casting, for example, involves multiple steps, including mold preparation, bronze pouring, and finishing. This process can take several weeks to months to complete, requiring patience and attention to detail.
What are the differences between lost wax casting, sand casting, and direct casting?
- Lost wax casting offers high precision and intricate details, making it ideal for lifelike sculptures.
- Sand casting uses compacted sand molds, which are faster and more cost-effective but less detailed.
- Direct casting skips mold-making and involves carving directly into materials like wax or clay, allowing for organic and experimental designs.
Each method has unique advantages, catering to different artistic needs.
How has technology influenced modern bronze casting?
Technology has revolutionized bronze casting by introducing tools like 3D modeling software and 3D printing. Artists can design intricate sculptures digitally and print wax or resin models for casting. Foundries use computer-aided systems to enhance precision, ensuring that the final piece reflects the artist’s vision. These advancements complement traditional methods, expanding creative possibilities.
What makes bronze casting suitable for public art?
Bronze casting is ideal for public art due to its durability and aesthetic appeal. Bronze sculptures withstand weathering and environmental factors, making them perfect for outdoor installations. The material’s versatility allows artists to create large-scale works that engage communities and enhance public spaces.
Where can I find more information or assistance with bronze casting?
For additional guidance, consider reaching out to local foundries, art schools, or community centers offering workshops. Online platforms like YouTube and Skillshare feature tutorials from experienced artists. If specific questions remain unanswered, contacting professionals or foundries directly can provide tailored advice and support.