What Are the Essential Materials for Brass Casting
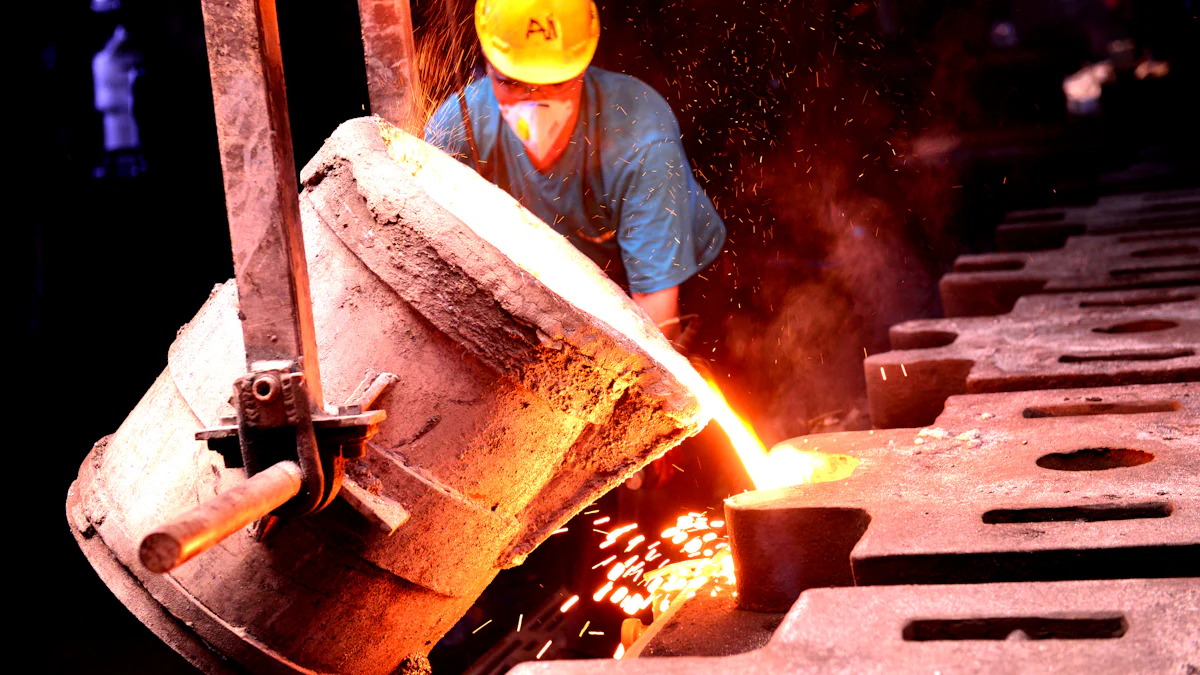
Brass casting transforms raw materials into intricate metalwork through a fascinating process. It demands precision and the right tools to achieve quality results. Brass, an alloy of copper and zinc, serves as the primary material, while flux ensures impurities are removed during melting. Molds shape the molten brass into desired forms. Tools like furnaces and crucibles handle extreme heat, making them indispensable in the brass casting process. Safety gear, including gloves and face shields, protects against high temperatures and molten metal hazards. In a Silicon Brass Precision Casting plant, the focus is on achieving high precision and quality in every casting. As experts say, understanding the science behind brass casting, including techniques used in Silicon Brass Precision Casting, helps minimize defects and ensures consistent, high-quality outcomes.
Key Takeaways
- Brass is the primary material for casting, with different alloys like yellow, red, and silicon brass suited for various applications.
- Using flux is essential to remove impurities during melting, ensuring a clean and high-quality final product.
- Choosing the right mold type, such as green sand or no-bake molds, is crucial for achieving the desired shape and detail in your castings.
- Invest in quality tools like furnaces, crucibles, and pouring tools to enhance safety and precision during the casting process.
- Always prioritize safety by wearing heat-resistant gear and ensuring proper ventilation to protect against harmful fumes.
- Start with small projects to build confidence and master the basics before tackling more complex brass casting designs.
- Engage with workshops or online communities to learn from experienced casters and accelerate your progress in brass casting.
Materials Needed for Brass Casting
Brass casting requires specific materials to ensure a smooth and successful process. Each material plays a unique role, contributing to the quality and precision of the final product. Let’s explore the essentials.
Brass
Types of brass alloys commonly used in casting
Brass, an alloy of copper and zinc, comes in various types, each suited for different casting needs. Yellow brass, known for its bright appearance, works well for decorative items. Red brass, with higher copper content, offers better corrosion resistance, making it ideal for plumbing fixtures. Silicon brass, often used in precision casting, provides excellent strength and durability. Choosing the right alloy depends on the project’s requirements, such as strength, appearance, or resistance to wear.
How to source brass for casting projects
Sourcing brass for casting projects can be straightforward. Scrap brass, like old plumbing parts or hardware, serves as a cost-effective option. Many metal suppliers also offer brass ingots specifically designed for casting. When purchasing, ensure the brass is free from contaminants to avoid impurities during the melting process. Local recycling centers or online marketplaces can also provide affordable options for obtaining brass materials.
Flux
The role of flux in removing impurities during the melting process
Flux plays a critical role in brass casting by removing impurities from molten metal. During the melting process, unwanted oxides and debris can form on the surface. Flux, when added, binds with these impurities, making them easier to skim off. This ensures the molten brass remains clean and produces a high-quality cast. Without flux, impurities could weaken the final product or create defects.
Common types of flux used in brass casting
Several types of flux are commonly used in brass casting. Borax, a popular choice, effectively removes oxides and prevents further oxidation. Commercial flux powders, specifically designed for brass casting, offer convenience and consistent results. Some casters even use homemade flux mixtures, combining borax with other materials like table salt. Selecting the right flux depends on personal preference and the specific requirements of the casting project.
Molds
Different types of molds (e.g., green sand molds, no-bake sand molds)
Molds shape molten brass into the desired form. Green sand molds, made from sand, clay, and water, are widely used for small to medium castings. They’re reusable and easy to prepare, making them a favorite among beginners. No-bake sand molds, created using sand and resin, provide greater strength and precision. These molds work well for larger or more detailed castings. Both types offer unique advantages, depending on the project’s complexity and size.
How to prepare molds for brass casting
Preparing molds for brass casting involves several steps. For green sand molds, mix sand, clay, and water until the consistency feels firm but pliable. Pack the mixture tightly around the pattern to create a detailed impression. For no-bake molds, combine sand with resin and a hardening agent, then shape it around the pattern. Allow the mold to cure before removing the pattern. Always ensure the mold is free from cracks or gaps to prevent leaks during pouring.
Tools Required for Brass Casting
Brass casting demands the right tools to ensure precision and safety. Each tool serves a specific purpose, contributing to the overall success of the process. Let’s dive into the essential tools needed for this craft.
Furnace
Types of furnaces suitable for brass casting
A furnace is the heart of any brass casting setup. It generates the intense heat required to melt brass, which typically occurs at temperatures exceeding 1,700°F (927°C). Two common types of furnaces are gas-fired and electric furnaces. Gas-fired furnaces are popular for their affordability and ability to reach high temperatures quickly. Electric furnaces, on the other hand, offer precise temperature control, making them ideal for projects requiring intricate details. Foundries often use specialized melting furnaces to maintain consistent heat, ensuring the brass melts evenly for high-quality results.
Tips for maintaining and operating a furnace
Proper maintenance extends the life of a furnace and ensures safe operation. Regularly inspect the furnace for cracks or wear in its lining, as these can lead to heat loss or accidents. Clean the furnace after each use to remove residue that might affect future casts. When operating the furnace, always monitor the temperature closely. Brass requires consistent heat to maintain its fluidity, so avoid letting the temperature drop during the process. Keeping fire extinguishers and fire blankets nearby adds an extra layer of safety.
Crucible
Materials used for crucibles and their heat resistance
The crucible holds the brass as it melts, so it must withstand extreme temperatures without breaking or contaminating the metal. Crucibles made from graphite or silicon carbide are common choices due to their excellent heat resistance and durability. These materials can endure temperatures well above 2,000°F (1,093°C), making them ideal for brass casting. A high-quality crucible ensures the molten brass remains pure and free from unwanted reactions during the melting process.
How to handle and care for a crucible
Handling a crucible requires caution. Always use tongs designed for high-temperature materials to avoid burns or accidents. Before each use, inspect the crucible for cracks or damage. A damaged crucible can fail under heat, leading to spills or contamination. After use, allow the crucible to cool naturally before cleaning it. Avoid using water to cool it down, as rapid temperature changes can cause it to crack. Proper care extends the life of the crucible and ensures consistent results.
Pouring Tools
Tools for safely pouring molten brass into molds
Pouring molten brass into molds is a delicate task that requires precision. Tools like pouring shanks and ladles help control the flow of the metal, reducing the risk of spills. These tools are designed to handle the weight and heat of molten brass, ensuring safety during the process. Vibratory equipment is sometimes used in foundries to remove finished castings from molds, but for smaller setups, manual pouring tools suffice.
Importance of precision during the pouring process
Precision during pouring directly impacts the quality of the final product. Careful control prevents air bubbles or impurities from entering the mold, which could weaken the casting. Pouring too quickly might cause splashing, while pouring too slowly could lead to incomplete fills. Maintaining a steady hand and focusing on the flow ensures the molten brass fills every detail of the mold. This step is crucial for achieving intricate designs and flawless results.
Additional Tools
Tongs for handling hot materials
Tongs are essential for safely managing hot materials during brass casting. They allow the caster to grip and move the crucible or other heated items without direct contact. High-quality tongs, made from heat-resistant metals, ensure durability and safety. These tools come in various designs, each tailored for specific tasks. For example, crucible tongs provide a secure grip on the crucible, while pouring tongs help control the flow of molten brass into molds. Regular inspection of tongs for wear or damage is crucial to avoid accidents. A sturdy pair of tongs not only enhances safety but also improves efficiency during the casting process.
Skimmers for removing impurities from molten brass
Skimmers play a vital role in maintaining the purity of molten brass. During the melting process, impurities like oxides and debris rise to the surface. A skimmer, designed with a flat or perforated edge, helps remove these unwanted materials. This step ensures the molten brass remains clean, resulting in a higher-quality cast. Skimmers must withstand extreme heat, so they are typically made from durable, heat-resistant materials. Using a skimmer effectively requires steady hands and attention to detail. By keeping the molten brass free from impurities, skimmers contribute to the overall success of the casting process.
Safety Gear
Heat-resistant gloves and aprons
Safety gear is non-negotiable in brass casting, and heat-resistant gloves and aprons top the list. Gloves protect hands from burns caused by handling hot tools or accidental splashes of molten brass. They are typically made from materials like leather or Kevlar, which can endure high temperatures. Aprons shield the body from heat and potential spills, offering an additional layer of protection. Investing in high-quality, well-fitted gloves and aprons ensures comfort and safety. Regularly checking for wear and tear is essential to maintain their effectiveness. Proper safety gear allows casters to focus on their craft without compromising their well-being.
Face shields and goggles for eye protection
Protecting the eyes is critical when working with molten brass. Face shields and goggles safeguard against sparks, heat, and accidental splashes. Goggles provide a snug fit, ensuring no debris or fumes reach the eyes, while face shields offer full-face coverage for added safety. Both are made from heat-resistant and shatterproof materials, designed to withstand the harsh conditions of brass casting. Wearing these protective items minimizes the risk of injuries and enhances visibility during the process. Clean and inspect them regularly to ensure they remain in good condition. With proper eye protection, casters can work confidently and safely.
Safety Equipment and Precautions
Safety should always come first in brass casting. The process involves high temperatures, molten metal, and potentially harmful fumes. Using the right equipment and following precautions can prevent accidents and ensure a smooth casting experience.
Protective Gear
Why heat-resistant clothing is essential
Heat-resistant clothing acts as a shield against extreme temperatures. Molten brass can splash unexpectedly, and regular clothing won’t provide enough protection. Materials like leather or Kevlar are excellent choices because they resist burns and heat damage. Wearing a heat-resistant apron and gloves ensures that the caster’s body and hands stay safe during every step of the process. This gear not only protects but also allows the caster to focus on their work without fear of injury.
The importance of proper footwear in a casting environment
Proper footwear is often overlooked but plays a crucial role in safety. Closed-toe shoes made from heat-resistant materials protect feet from accidental spills of molten brass. Steel-toed boots add an extra layer of protection, especially in environments where heavy tools or materials are handled. Slippery surfaces can also be a hazard, so footwear with non-slip soles helps maintain stability. Investing in the right shoes ensures safety and comfort throughout the casting process.
Ventilation
Ensuring proper airflow to avoid inhaling harmful fumes
Brass casting produces fumes that can be harmful if inhaled. Proper ventilation is essential to maintain a safe workspace. Open windows and doors help circulate fresh air, reducing the concentration of fumes. For indoor setups, installing exhaust fans or ventilation systems ensures that toxic gases don’t linger. A well-ventilated area not only protects the caster’s health but also creates a more comfortable working environment.
Using fume extractors or working in open spaces
Fume extractors are valuable tools for removing harmful particles from the air. These devices capture and filter fumes directly at the source, making them ideal for small workshops. For those without access to extractors, working in open spaces is a practical alternative. Outdoor environments allow fumes to disperse naturally, minimizing exposure. Whether using extractors or working outside, prioritizing clean air is a must for safe brass casting.
Handling Molten Metal
Tips for safely handling and pouring molten brass
Handling molten brass requires precision and care. Always use tools like tongs and pouring ladles designed for high temperatures. Keep a steady hand when pouring to avoid splashes or spills. Position the mold securely to prevent movement during the pour. It’s also wise to rehearse the pouring process with cold materials to build confidence. Staying focused and prepared ensures a safer experience when working with molten metal.
Common mistakes to avoid during the casting process
Mistakes during brass casting can lead to accidents or flawed results. One common error is rushing the process, which increases the risk of spills or incomplete molds. Neglecting to preheat the mold can cause the molten brass to cool too quickly, leading to defects. Another mistake is wearing improper safety gear, leaving the caster vulnerable to burns or injuries. Avoiding these pitfalls requires patience, preparation, and attention to detail.
Tips for Beginners
Starting with brass casting can feel overwhelming, but breaking it into manageable steps makes the journey enjoyable. Beginners should focus on building confidence and mastering the basics before diving into complex projects. Here are some practical tips to help you get started.
Start Small
Why beginners should start with small projects
Small projects provide an excellent starting point for beginners. They require fewer materials, tools, and time, making them less intimidating. Creating simple items like keychains or small decorative pieces allows beginners to familiarize themselves with the process without feeling overwhelmed. Starting small also reduces the risk of wasting materials if mistakes occur, which is common when learning a new skill.
“Every expert was once a beginner.” Small steps lead to big achievements in brass casting.
Learning the basics before moving to complex designs
Mastering the basics lays the foundation for success. Beginners should focus on understanding how to melt brass, prepare molds, and pour molten metal safely. These fundamental skills are essential for tackling more intricate designs later. Practicing with straightforward patterns helps build muscle memory and confidence. Once the basics feel natural, transitioning to detailed and complex projects becomes much easier.
Practice Safety First
Double-checking safety gear before starting
Safety should always come first in brass casting. Before beginning any project, ensure all safety gear is in place and functioning properly. Heat-resistant gloves, aprons, and face shields protect against burns and splashes. Proper footwear, like steel-toed boots, guards against accidental spills. Taking a moment to double-check your gear minimizes risks and ensures a safer experience.
Personal protective equipment isn’t optional—it’s essential for every brass casting session.
Practicing with cold runs to understand the process
Cold runs, or practice sessions without heat, are invaluable for beginners. They allow you to rehearse each step of the process, from handling tools to pouring into molds, without the pressure of working with molten metal. This practice helps identify potential mistakes and builds familiarity with the tools. By the time you work with actual molten brass, you’ll feel more prepared and confident.
Learn from Others
Joining workshops or online communities for guidance
Learning from experienced casters accelerates progress. Workshops offer hands-on experience under the guidance of professionals, while online communities provide a wealth of shared knowledge. Platforms like forums, social media groups, and dedicated websites connect beginners with seasoned experts. These spaces encourage questions, share tips, and celebrate successes, creating a supportive environment for learning.
Collaboration and shared experiences make the brass casting journey more rewarding.
Watching tutorials and reading guides for additional tips
Tutorials and guides serve as excellent resources for beginners. Video tutorials demonstrate techniques visually, making it easier to understand complex steps. Written guides provide detailed explanations and troubleshooting tips. Combining these resources with hands-on practice ensures a well-rounded learning experience. Beginners can revisit these materials whenever they need clarification or inspiration.
Brass casting offers a unique blend of creativity and craftsmanship. Success begins with gathering the right materials and tools while prioritizing safety at every step. Beginners should start small, focusing on mastering the basics before tackling complex designs. A well-prepared workspace, as emphasized by experts like Dongguan Shengen Metal Co., Ltd, ensures smoother results. Learning from others, whether through workshops or online communities, accelerates progress. As Alvaro Mendoza, PhD suggests, attention to detail and consistent practice build confidence and skill. With preparation and patience, anyone can enjoy the rewarding art of brass casting.
FAQ
What is the most important material for brass casting?
Brass serves as the primary material in brass casting. It is an alloy made from copper and zinc, offering versatility for various applications. The specific type of brass alloy chosen depends on the project’s requirements, such as strength, corrosion resistance, or appearance.
Why is flux necessary in brass casting?
Flux plays a vital role in removing impurities during the melting process. It binds with oxides and debris, making them easier to skim off the molten brass. This step ensures the final product remains strong and free from defects.
What types of molds are best for beginners?
Green sand molds are ideal for beginners. They are easy to prepare and reuse, making them cost-effective. These molds consist of sand, clay, and water, providing flexibility for small to medium projects. Beginners can also experiment with no-bake molds for more detailed designs.
How can beginners ensure safety while brass casting?
Safety starts with proper gear. Heat-resistant gloves, aprons, and face shields protect against burns and splashes. Closed-toe shoes with non-slip soles prevent injuries from spills or slippery surfaces. Beginners should also work in well-ventilated areas to avoid inhaling harmful fumes.
What tools are essential for brass casting?
Key tools include a furnace for melting brass, a crucible to hold the molten metal, and pouring tools like ladles or shanks. Additional tools, such as tongs and skimmers, help handle hot materials and remove impurities. Each tool contributes to the precision and safety of the process.
How can beginners practice brass casting without risks?
Cold runs offer a safe way to practice. These involve rehearsing each step of the process without using heat or molten metal. Beginners can familiarize themselves with tools, mold preparation, and pouring techniques, building confidence before working with actual brass.
Why is proper ventilation important in brass casting?
Brass casting produces fumes that can be harmful if inhaled. Proper ventilation ensures clean airflow, reducing exposure to toxic gases. Options include working in open spaces or using fume extractors in indoor setups. A well-ventilated workspace protects health and enhances comfort.
What are common mistakes to avoid in brass casting?
Rushing the process often leads to errors. Skipping mold preheating can cause the molten brass to cool too quickly, resulting in defects. Using improper safety gear increases the risk of injuries. Beginners should focus on preparation, patience, and attention to detail to avoid these pitfalls.
How does mold design affect the quality of brass casting?
Mold design directly impacts the final product’s quality. A well-formed mold ensures the molten brass fills every detail, creating accurate and high-quality parts. Careful preparation and inspection of molds prevent leaks or imperfections during the casting process.
Can scrap brass be used for casting projects?
Yes, scrap brass is a cost-effective option for casting. Items like old plumbing fixtures or hardware can be melted down and reused. However, it is crucial to ensure the scrap is free from contaminants to avoid impurities in the final cast.