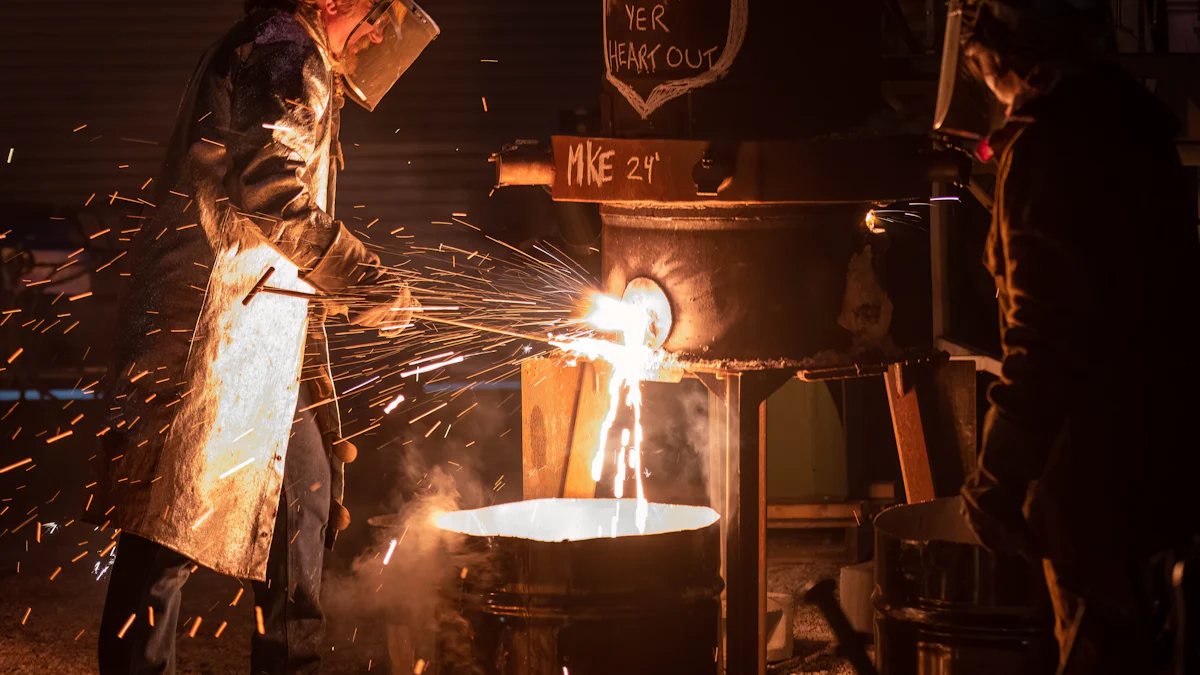
Silicon bronze precision casting is a remarkable process that highlights the unique properties of this copper-based alloy, which is prized for its strength, corrosion resistance, and workability. The composition of silicon bronze, enriched with silicon, ensures exceptional durability and performance in demanding environments. Industries rely on this alloy for its ability to produce intricate designs with ease, particularly in bronze casting applications. The fluidity of silicon bronze during investment casting allows manufacturers to create detailed components with minimal defects. Additionally, its minimal cooling contraction further enhances its suitability for precision casting, making it a preferred choice for applications that require both complexity and reliability.
Key Takeaways
- Silicon bronze is renowned for its strength and durability, making it ideal for precision casting in demanding industries like marine hardware and aerospace.
- The alloy’s exceptional corrosion resistance ensures longevity, allowing components to withstand harsh environments without degrading.
- Silicon bronze’s excellent workability and fluidity enable manufacturers to create intricate designs with minimal defects, enhancing both aesthetic and functional quality.
- Its minimal cooling contraction reduces the risk of defects such as warping or cracking, ensuring that the final product retains its intended shape.
- Silicon bronze is versatile, suitable for a wide range of applications from art and sculpture to industrial machinery and architectural elements.
- The cost-effectiveness of silicon bronze comes from its durability and reduced maintenance needs, making it a smart investment for long-term use.
- Embracing silicon bronze precision casting allows manufacturers to achieve high-quality results while preserving the legacy of traditional craftsmanship.
Properties of Silicon Bronze for Precision Casting
Strength and Durability
Silicon bronze stands out for its impressive strength and durability, making it a reliable choice for precision casting. This alloy, composed primarily of copper with silicon as a key additive, offers high tensile and yield strength. These properties ensure that components made from silicon bronze can withstand significant stress without deforming or breaking. Industries that demand long-lasting materials, such as marine hardware and industrial machinery, benefit greatly from its robust nature. Whether used in architectural elements or mechanical parts, silicon bronze delivers consistent performance over time.
Corrosion Resistance
One of the most notable features of silicon bronze is its exceptional resistance to corrosion. This property makes it particularly valuable in environments exposed to moisture, chemicals, or saltwater. For example, marine applications like propeller shafts and fasteners rely on silicon bronze to endure the harsh effects of seawater. Its ability to resist rust and degradation ensures that components maintain their integrity even in challenging conditions. This corrosion resistance also makes it a preferred material for outdoor fixtures and sculptures, where exposure to the elements is inevitable.
“Silicon bronze ensures lasting durability, particularly in a corrosive medium such as seawater,” highlighting its unmatched reliability in harsh environments.
Workability and Malleability
Silicon bronze offers excellent workability and malleability, making it a favorite among manufacturers and artists alike. Its lower melting point allows for easier casting, enabling the creation of intricate shapes with minimal defects. Sculptors appreciate its ability to capture fine details, while manufacturers value its adaptability for complex designs. Additionally, its malleability ensures that it can be shaped and formed without compromising its structural integrity. This combination of ease of use and reliability makes silicon bronze an indispensable material for precision casting.
Exceptional Fluidity and Cooling Characteristics
Silicon bronze stands out in precision casting due to its exceptional fluidity and cooling characteristics. This alloy flows effortlessly into molds, filling even the most intricate details with remarkable accuracy. Its low melting point enhances this fluidity, allowing manufacturers to achieve high-quality results with minimal effort. Whether creating delicate sculptures or complex industrial components, silicon bronze ensures that every detail is captured with precision.
During the cooling process, silicon bronze exhibits minimal contraction. This unique property reduces the risk of defects like warping or cracking, which can compromise the integrity of the final product. Manufacturers value this stability because it ensures consistent results, even in large-scale production. The combination of fluidity and controlled cooling makes silicon bronze a reliable choice for applications requiring both complexity and durability.
“Silicon bronze’s lower melting point and fluidity allow for the creation of intricate shapes with minimal defects,” highlighting its superiority in casting processes.
This alloy also offers a smooth surface finish, reducing the need for extensive post-casting work. Artists and engineers alike appreciate this feature, as it saves time and resources while maintaining the aesthetic and functional quality of the cast. From marine hardware to architectural elements, silicon bronze delivers unparalleled performance in precision casting.
Benefits of Silicon Bronze Precision Casting
High-Quality Detail Reproduction
Silicon bronze excels in capturing intricate details during the casting process. Its exceptional fluidity allows the molten alloy to flow seamlessly into molds, filling even the most complex designs with precision. This characteristic ensures that every curve, edge, and texture is faithfully reproduced. Whether crafting delicate sculptures or industrial components, manufacturers achieve remarkable accuracy with silicon bronze.
Additionally, its minimal cooling contraction reduces the risk of defects like cracks or warping. This stability ensures that the final product retains its intended shape and dimensions. Artists and engineers alike appreciate how silicon bronze delivers a flawless finish, reducing the need for extensive post-casting work. The result? Components that combine both aesthetic appeal and functional excellence.
“Silicon bronze’s ability to flow smoothly into molds ensures high precision and reduces the risk of defects,” making it a top choice for detailed designs.
Longevity and Resistance to Wear
Durability defines silicon bronze. This alloy resists wear and tear, even in demanding environments. Its strength ensures that components can handle heavy loads and constant use without degrading. Industries like marine hardware and aerospace rely on silicon bronze for its ability to endure harsh conditions while maintaining performance.
Corrosion resistance further enhances its longevity. Silicon bronze withstands exposure to moisture, chemicals, and saltwater, making it ideal for outdoor and marine applications. For example, propeller shafts and fasteners crafted from silicon bronze remain reliable despite prolonged contact with seawater. This resilience ensures that products last longer, reducing the need for frequent replacements and saving costs over time.
Versatility Across Applications
The versatility of silicon bronze makes it indispensable across various industries. Its unique combination of strength, corrosion resistance, and workability allows it to adapt to diverse applications. In the art world, sculptors use silicon bronze to create intricate and expressive pieces. Its ability to capture fine details brings artistic visions to life.
In marine environments, silicon bronze proves invaluable for crafting durable hardware like rudders and steering gear. Its resistance to corrosion ensures these critical components function reliably in harsh conditions. The aerospace industry values silicon bronze for its strength and self-lubricating properties, making it suitable for high-performance parts like bearing cages. Even in architecture, silicon bronze harmonizes form and function, offering both structural integrity and aesthetic appeal.
From industrial machinery to decorative elements, silicon bronze precision casting delivers unmatched versatility. Its adaptability ensures that it meets the needs of both traditional craftsmanship and modern engineering.
Cost-Effectiveness in Long-Term Use
Silicon bronze offers a unique combination of durability and efficiency, making it a cost-effective choice for long-term use. Its exceptional strength ensures that components crafted from this alloy can withstand heavy loads and continuous wear without frequent replacements. Industries that rely on high-performance materials, such as marine hardware and aerospace, benefit significantly from the reduced maintenance costs associated with silicon bronze.
The alloy’s corrosion resistance further enhances its economic value. Unlike other materials that degrade quickly in harsh environments, silicon bronze maintains its integrity even when exposed to moisture, chemicals, or saltwater. For example, marine applications like propeller shafts and fasteners crafted from silicon bronze remain reliable over extended periods. This longevity reduces the need for costly repairs or replacements, saving both time and resources.
“Silicon bronze ensures lasting durability, particularly in a corrosive medium such as seawater,” highlighting its unmatched reliability in challenging conditions.
Another factor contributing to its cost-effectiveness is its ease of casting. Silicon bronze flows smoothly into molds, capturing intricate details with minimal defects. This reduces the need for extensive post-casting work, saving labor and material costs. Additionally, its minimal cooling contraction ensures consistent results, even in large-scale production. Manufacturers can rely on silicon bronze to deliver high-quality components without incurring additional expenses for corrections or adjustments.
The alloy’s versatility also plays a role in its economic appeal. From sculptures to industrial machinery, silicon bronze adapts to various applications, eliminating the need for multiple specialized materials. Its ability to combine strength, corrosion resistance, and aesthetic appeal in a single material streamlines production processes and reduces overall costs.
In the long run, silicon bronze proves to be an investment rather than an expense. Its durability, resistance to wear, and adaptability ensure that it delivers value across industries. Whether used in art, architecture, or engineering, silicon bronze remains a reliable and cost-effective choice for precision casting.
Applications of Silicon Bronze Precision Casting
Art and Sculpture
Silicon bronze has become a favorite material for artists and sculptors. Its ability to capture intricate details makes it ideal for creating expressive and lifelike sculptures. The alloy’s exceptional fluidity allows molten silicon bronze to flow seamlessly into molds, ensuring even the most delicate features are preserved. Artists value its smooth surface finish, which reduces the need for extensive polishing or post-casting work.
This material also offers durability and resistance to environmental factors. Outdoor sculptures crafted from silicon bronze maintain their beauty despite exposure to rain, wind, or sunlight. Its corrosion resistance ensures that these works of art stand the test of time, making it a reliable choice for public installations and monuments. Sculptors appreciate how silicon bronze combines aesthetic appeal with long-lasting performance.
“Silicon bronze’s ability to capture fine details and resist corrosion makes it a top choice for artistic creations,” highlighting its role in the art world.
Marine Hardware
Marine environments demand materials that can withstand harsh conditions, and silicon bronze excels in this regard. Its superior corrosion resistance makes it perfect for crafting marine hardware like propeller shafts, rudders, and fasteners. Unlike other materials, silicon bronze resists the damaging effects of saltwater, ensuring components remain functional and reliable over time.
The alloy’s strength and wear resistance further enhance its suitability for marine applications. Components made from silicon bronze can handle heavy loads and constant use without degrading. Its self-lubricating properties also reduce friction, improving the performance of moving parts like bearings and gears. These qualities make silicon bronze an indispensable material for shipbuilding and other marine industries.
Additionally, silicon bronze offers a lower melting point, which simplifies the casting process. Manufacturers can produce complex shapes with minimal defects, ensuring high-quality results. This ease of casting, combined with its durability, makes silicon bronze a cost-effective solution for marine hardware.
Aerospace Components
The aerospace industry relies on materials that deliver both strength and precision, and silicon bronze meets these demands. Its high tensile and yield strength ensure that components can endure extreme stress and pressure. This makes it suitable for critical parts like bearing cages, raceways, and spacers.
Silicon bronze’s self-lubricating properties provide an added advantage in aerospace applications. Moving parts crafted from this alloy experience reduced friction, enhancing their efficiency and lifespan. Its non-magnetic nature also makes it ideal for sensitive equipment where magnetic interference must be avoided.
Corrosion resistance plays a vital role in aerospace environments, where exposure to moisture and chemicals is common. Silicon bronze maintains its integrity under these conditions, ensuring the reliability of components. Its ease of casting allows manufacturers to produce intricate designs with precision, meeting the exacting standards of the aerospace industry.
“Silicon bronze combines strength, corrosion resistance, and precision, making it a trusted material for aerospace components,” emphasizing its importance in advanced engineering.
Industrial and Architectural Elements
Silicon bronze plays a vital role in industrial and architectural applications, offering a unique blend of strength, durability, and aesthetic appeal. Its mechanical properties make it a reliable choice for structural components, while its visual qualities enhance the beauty of architectural designs.
In industrial settings, silicon bronze stands out for its ability to handle heavy loads and resist wear. Manufacturers use it to create gears, bushings, and other machinery parts that require both strength and precision. Its self-lubricating properties reduce friction, improving the efficiency and lifespan of moving components. Compared to other bronze alloys, silicon bronze offers higher tensile strength and better wear resistance, making it a preferred material for demanding environments.
Architectural elements crafted from silicon bronze combine functionality with elegance. Designers often choose this alloy for decorative features like railings, door handles, and light fixtures. Its corrosion resistance ensures these elements maintain their appearance and integrity, even when exposed to outdoor conditions. The smooth surface finish of silicon bronze adds a polished look, reducing the need for extensive maintenance.
“Silicon bronze’s appealing surface finish and superior corrosion resistance make it ideal for both industrial and architectural applications,” highlighting its versatility across these fields.
Another advantage of silicon bronze lies in its ease of casting. Its lower melting point allows for the creation of intricate designs with minimal defects. This makes it possible to produce detailed architectural ornaments or complex industrial parts efficiently. The alloy’s minimal cooling contraction ensures consistent results, even in large-scale production.
When compared to other materials, silicon bronze offers unmatched versatility. It provides the strength needed for industrial use and the aesthetic qualities desired in architecture. Its ability to adapt to various applications makes it an invaluable resource for engineers, architects, and designers alike.
The Precision Casting Process with Silicon Bronze
Creating the Mold
The precision casting process begins with creating a mold, which serves as the blueprint for the final product. Manufacturers typically use wax or similar materials to craft a detailed model of the desired component. This model captures every intricate feature, ensuring the final cast mirrors the original design. Once the model is ready, it gets coated with a ceramic slurry. This coating hardens to form a robust shell, capable of withstanding the high temperatures of molten silicon bronze.
After the ceramic shell solidifies, the wax inside is melted and drained, leaving behind a hollow cavity. This cavity becomes the mold for the silicon bronze. The precision of this step is critical. Any imperfections in the mold can transfer to the final product, affecting its quality. By focusing on accuracy during mold creation, manufacturers ensure that the casting process delivers components with flawless detail.
“The mold acts as the foundation of precision casting, capturing every detail to ensure a perfect final product.”
Melting and Pouring Silicon Bronze
Once the mold is ready, the next step involves melting the silicon bronze. This alloy melts at a relatively low temperature compared to other metals, making it easier to handle during casting. The molten silicon bronze achieves exceptional fluidity, allowing it to flow smoothly into the mold. This property ensures that even the most intricate designs are filled without gaps or defects.
Manufacturers carefully pour the molten alloy into the mold, ensuring it reaches every corner of the cavity. Precision during this step is vital. Uneven pouring can lead to air pockets or incomplete fills, compromising the integrity of the final product. The controlled pouring process highlights the importance of expertise in silicon bronze precision casting. By maintaining steady hands and a keen eye, manufacturers achieve remarkable results.
“Silicon bronze’s fluidity ensures that every corner of the mold is filled, capturing even the smallest details with precision.”
Cooling and Solidification
After pouring, the molten silicon bronze begins to cool and solidify. This stage is crucial for determining the strength and durability of the final product. Silicon bronze exhibits minimal cooling contraction, which reduces the risk of defects like warping or cracking. This unique property ensures that the cast retains its intended shape and dimensions.
The cooling process must occur gradually to prevent internal stresses within the material. Rapid cooling can lead to brittleness, while uneven cooling may cause structural weaknesses. Manufacturers often use controlled environments to regulate the cooling rate, ensuring consistent results. Once the silicon bronze fully solidifies, the ceramic mold is broken away, revealing the cast component.
The final product undergoes inspection to ensure it meets quality standards. Any minor imperfections are addressed during finishing, but the precision of the casting process often minimizes the need for extensive post-casting work. This efficiency makes silicon bronze precision casting a preferred choice for industries requiring high-quality, durable components.
“Minimal cooling contraction in silicon bronze ensures that the final product remains true to its design, free from defects.”
Finishing and Quality Control
The finishing and quality control stage ensures that every silicon bronze casting meets the highest standards of precision and durability. This step transforms raw castings into polished, functional components ready for use in various applications. Manufacturers focus on refining the surface, inspecting for defects, and verifying the product’s adherence to specifications.
1. Surface Refinement
After removing the ceramic mold, the casting undergoes surface treatment to achieve a smooth and polished finish. Technicians use grinding, sanding, or polishing tools to eliminate any rough edges or imperfections. This process enhances the aesthetic appeal of the component, which is especially important for sculptures, architectural elements, and decorative hardware. For industrial parts, a refined surface ensures better performance and compatibility with other components.
2. Dimensional Accuracy Check
Precision is critical in silicon bronze casting. Manufacturers measure the dimensions of the finished product against the original design specifications. Advanced tools like calipers, micrometers, or coordinate measuring machines (CMM) help verify accuracy. Any deviations are corrected during this stage to ensure the component fits seamlessly into its intended application.
3. Defect Inspection
Casting defects, such as air pockets, cracks, or inclusions, can compromise the integrity of the final product. Quality control teams conduct thorough inspections to identify and address these issues. Non-destructive testing methods, like X-ray or ultrasonic testing, allow technicians to detect internal flaws without damaging the component. By resolving defects early, manufacturers ensure the reliability and longevity of the casting.
4. Functional Testing
For components used in demanding environments, functional testing is essential. Manufacturers simulate real-world conditions to evaluate the casting’s performance. For example, marine hardware undergoes corrosion resistance tests, while aerospace parts are tested for strength and wear resistance. These tests confirm that the silicon bronze casting can withstand the stresses of its intended application.
“Quality control ensures that every silicon bronze casting delivers both aesthetic and functional excellence,” emphasizing the importance of this final step.
5. Final Approval and Packaging
Once the casting passes all inspections and tests, it receives final approval. The component is then cleaned, labeled, and packaged for delivery. Proper packaging protects the casting during transportation, ensuring it reaches the customer in perfect condition.
The finishing and quality control process highlights the meticulous attention to detail required in silicon bronze precision casting. By investing time and effort into this stage, manufacturers deliver products that combine beauty, durability, and functionality.
Silicon bronze stands as a cornerstone in precision casting, offering unmatched strength, corrosion resistance, and versatility. Its ability to produce intricate, durable components has made it a preferred material across industries like marine hardware, art, and aerospace. The alloy’s exceptional fluidity and minimal cooling contraction ensure consistent, high-quality results. By embracing silicon bronze precision casting, manufacturers unlock the potential for creating reliable, long-lasting products. This alloy’s unique properties not only meet the demands of modern engineering but also preserve its legacy in traditional craftsmanship, making it indispensable for both innovation and artistry.
FAQ
What is silicon bronze made of?
Silicon bronze is primarily a copper-based alloy with a small percentage of silicon, typically around 2.5% to 6%. It may also include other elements like manganese, zinc, or tin to enhance its properties. This unique composition gives it strength, corrosion resistance, and excellent casting characteristics.
Why is silicon bronze preferred for precision casting?
Silicon bronze offers exceptional fluidity when molten, allowing it to fill intricate molds with ease. Its minimal cooling contraction ensures that the final product retains its shape and dimensions without defects like warping or cracking. These qualities make it ideal for creating detailed and durable components.
How does silicon bronze resist corrosion?
Silicon bronze forms a protective oxide layer on its surface when exposed to the environment. This layer prevents further oxidation and protects the material from moisture, chemicals, and saltwater. Its corrosion resistance makes it a popular choice for marine hardware and outdoor applications.
What industries commonly use silicon bronze?
Silicon bronze is widely used across various industries, including:
- Marine hardware: Propeller shafts, rudders, and fasteners.
- Aerospace: Bearing cages, raceways, and spacers.
- Art and sculpture: Intricate statues and decorative pieces.
- Architecture: Railings, door handles, and light fixtures.
- Industrial machinery: Gears, bushings, and other high-wear components.
Its versatility allows it to adapt to both functional and aesthetic applications.
Is silicon bronze suitable for outdoor use?
Yes, silicon bronze is highly suitable for outdoor use. Its corrosion resistance ensures that it withstands exposure to rain, sunlight, and even saltwater. This durability makes it a preferred material for sculptures, architectural elements, and marine hardware.
How long has silicon bronze been in use?
Silicon bronze has a rich history dating back centuries. Historically, it was used for tools, weapons, and ship fittings due to its strength and resistance to harsh environments. Over time, its applications expanded to include marine hardware, architectural embellishments, and industrial components.
“Silicon bronze’s legacy in craftsmanship and engineering highlights its enduring value across generations.”
Can silicon bronze be used for artistic purposes?
Absolutely! Artists and sculptors favor silicon bronze for its ability to capture fine details and its smooth surface finish. Its workability allows for the creation of intricate designs, while its durability ensures that sculptures maintain their beauty over time, even in outdoor settings.
What makes silicon bronze cost-effective?
Silicon bronze combines durability, corrosion resistance, and ease of casting, reducing the need for frequent replacements or extensive post-casting work. Its longevity in harsh environments and adaptability across applications make it a cost-effective choice for both manufacturers and end-users.
How does silicon bronze compare to other bronze alloys?
Silicon bronze stands out for its superior corrosion resistance and strength. Unlike other bronze alloys, it offers exceptional fluidity during casting and minimal cooling contraction. These properties make it a preferred material for precision casting and applications requiring intricate designs.
What are some historical uses of silicon bronze?
Historically, silicon bronze was used for:
- Ship fittings and fasteners: Its corrosion resistance made it ideal for marine environments.
- Tools and weapons: Its strength and durability ensured reliability in demanding conditions.
- Architectural elements: Outdoor fixtures and decorative features benefited from its aesthetic appeal and resistance to weathering.
- Chemical industry: Originally developed for its excellent casting properties, it found use in chemical-resistant components.
These historical applications highlight its versatility and enduring value across industries.